Insulating Varnishes
Insulating Varnishes
Our insulating varnishes are meticulously crafted to protect your electrical components with unmatched durability and reliability. Whether you require electrical insulating varnish for intricate applications or robust protection, our products offer superior performance and durability.
Cenvar varnishes provide high tank stability, fast curing, excellent film forming ability and high insulating performance. Ensure smooth operation of your equipment with our specialized solutions, tailored to meet the highest industry standards.
Types of Insulating Varnishes
Solvent Based Insulating Varnishes
These essential secondary insulations for electrical and electronic equipment are typically resin-based materials (such as alkyd, phenolic, epoxy, polyurethane, silicone, polyamide, and polyamide- imide) which are dissolved in non-reactive organic solvents.
They can be applied through various methods such as dipping, brushing, spraying, dip & oven bake, conveyorized dip and bake systems, or vacuum impregnation, depending on the component size and equipment requirements.
Curing can occur at room temperature (air dry) or be accelerated by heat (oven baking).
Water Based Insulating Varnishes
These are akin to solvent based varnishes, but instead of using solvents, the resins are dissolved in water with an eco-friendlier co-solvent. This type of product also utilizes emulsion technology.
With a low environmental impact, these materials often provide a cost-effective solution for replacing traditional solvent-based varnish technology.
The decision between solvent-based and water-based varnishes often hinges on specific application requirements and environmental considerations.
Finishing & Anti-Tracking Insulating Varnishes
These finishing varnishes are utilized to improve track resistance, coil bonding, and resistance to humidity and chemicals. Additionally, they enhance the aesthetics of the equipment.
These varnishes, which can be applied by spray, brush, or pour and dip methods, are available in various pigmented colours (red, grey, blue, white, and black). They provide a thicker, glossy & opaque film.
Finishing & Anti-Tracking Insulating Varnishes
These finishing varnishes are utilized to improve track resistance, coil bonding, and resistance to humidity and chemicals. Additionally, they enhance the aesthetics of the equipment.
These varnishes, which can be applied by spray, brush, or pour and dip methods, are available in various pigmented colours (red, grey, blue, white, and black). They provide a thicker, glossy & opaque film.
Insulating Varnishes Applications
- Anti Tracking
- Pigmented Finishing (Red, Grey, Black)
- Core Plate (Solvented & Water base)
- Sleeving & Fibre Glass Conductors
- Ballast / Choke (White)
- Conformal / PCB Coatings
- Structural Coatings
Key Benefits of Insulating Varnishes
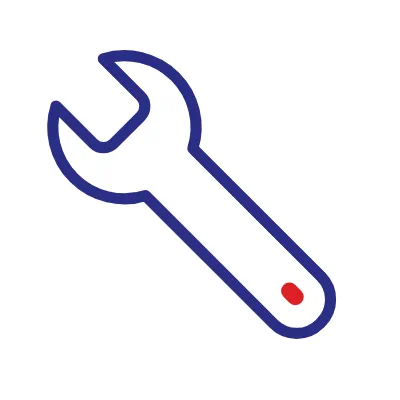
Enhanced Mechanical Bonding & Cohesion
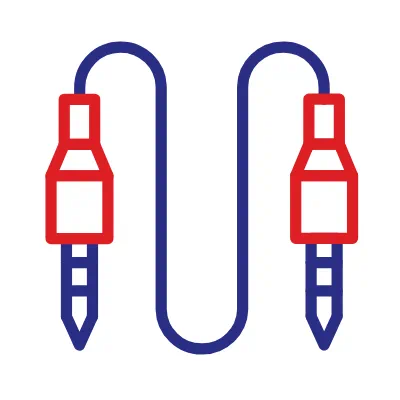
Superior Electrical Properties
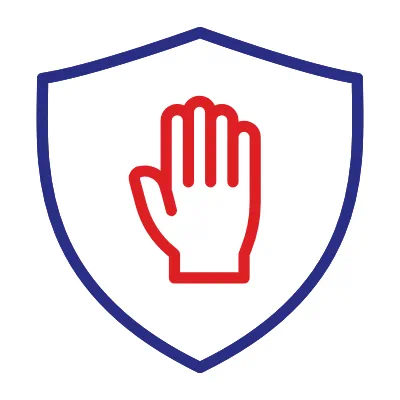
Effective Anti-Tracking & Leakage Current Prevention
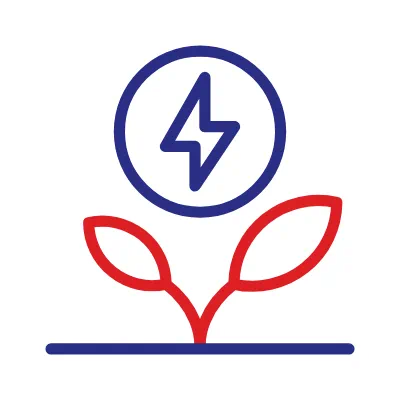
Environmental Protection Against Moisture, Mold, Dust, Heat
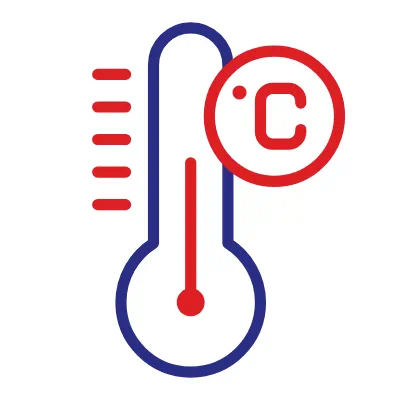
Available for
Higher Thermal Class Applications up to 220°C
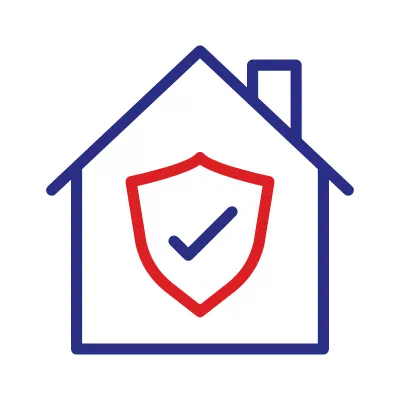
High Flash Point Variants
Product Range
Air Dry
Anti Tracking Varnishes
⮞ Alkyd, Phenolic, Epoxy
⮞ Clear, Golden Transparent film
⮞ Hard, Flexible
⮞ High & Low Viscosities
⮞ High Flash Point
Pigmented Air Dry Finishing Varnishes
⮞ Red, Grey, Blue, White, Black
⮞ Alkyd, Phenolic, Epoxy
⮞ High & Low Viscosities and Gelcoats
⮞ High Flash Point
Baking Varnishes
⮞ Alkyd, Phenolic, Epoxy, Polyesterimide, Silicone, Polyurethane, Polyamide Imide
⮞ Clear, Golden Transparent film
⮞ Hard, Flexible
⮞ High & Low Viscosities
⮞ High Flash Point
Water Based Varnishes
⮞ Alkyd, Phenolic, Epoxy
⮞ Clear, Golden Transparent film
⮞ Hard, Flexible
⮞ High & Low Viscosities
⮞ High Flash Point
Flexible Varnishes
⮞ Alkyd, Phenolic, Polyester, Polyurethane, Polyesterimide, Epoxy
⮞ Clear, Golden Transparent film
⮞ High & Low Viscosities
⮞ High Flash Point
Core Plate, Lamination Varnishes
⮞ Coreplate Insulation C3 & C6
⮞ White, Off-White, Grey, Clear, Black
⮞ Alkyd, Phenolic, Epoxy, Water Based
⮞ High & Low Viscosities
⮞ High Flash Point
Binder Varnishes for Fiberglass Conductors
⮞ Clear, Golden transparent film
⮞ Polyester, Polyesterimide, Polyurethane, Epoxy
⮞ High & Low Viscosities
⮞ High Flash Point
⮞ High Bond Strength, High Flexibility
Varnishes for
Choke / Ballasts
⮞ White, Off-White
⮞ Alkyd, Phenolic, Epoxy
⮞ High & Low Viscosities
⮞ High Flash Point
Conformal Coatings
⮞ Alkyd, Phenolic, Epoxy
⮞ Clear, Golden Transparent film, Opaque black
⮞ Hard, Flexible
⮞ High & Low Viscosities
⮞ High Flash Point
Structural, Protective Coatings
⮞ Alkyd, Phenolic, Epoxy
⮞ Clear, Golden Transparent film, Opaque black, red
⮞ Hard, Semi-Flexible
⮞ High, Low Viscosities & Gelcoats
⮞ High Flash Point
FAQs
Cenvar offers a comprehensive range of insulating varnishes, including alkyd, phenolic, epoxy, polyurethane, silicone, polyamide-imide, and water-based varnishes, tailored to meet diverse industrial needs.
Yes, we offer water-based varnishes and emulsions suitable for applications up to Thermal Class H.
Cenvar’s insulating varnishes and Chetak wires are available in various thermal classes, including Class 130, 155, 180, 200, and 220, ensuring suitability for different temperature requirements in industrial applications.
Yes, Cenvar prioritizes sustainability. Our varnishes are formulated to minimize environmental impact, with options for low VOC emissions and compliance with environmental regulations.
Water-based varnishes contain water and eco-friendly co-solvents. Compared to regular solvent-based varnishes, they have a lower environmental impact, higher flash points, and are easier to store and handle. They also produce less odour, contributing to a better working atmosphere.
Safety is paramount at Cenvar. We adhere to strict safety protocols and standards in our production facilities, ensuring a safe working environment for our employees and maintaining product integrity.
Insulating varnishes can be applied using various methods, including dipping, brushing, spraying, dip & oven bake, conveyorised dip and bake systems, or vacuum impregnation. The choice of method depends on factors such as component size, available equipment, cost, and desired properties.
Available sizes: 200 ml, 500 ml, 1 litre, 5 litres, and 30 litres.
Oven Baking! Oven baking offers a faster, more thorough cure, penetrating deep into the coil for superior bonding and insulating properties. It delivers better overall performance, with pricing comparable to air-drying varnishes.
Yes, Cenvar offers custom formulations tailored to meet specific customer needs. Our team works closely with clients to develop varnishes that meet unique performance and application requirements.
- Primary Insulation: This is the main barrier that prevents electrical current from flowing between the conductor windings (copper or aluminium). It includes wire enamels and coatings applied directly to the conductors.
- Secondary Insulation: This provides additional protection and acts as a backup to the primary insulation. It ensures that even if the primary insulation fails, there is an extra layer to prevent electrical faults. This includes insulating varnishes and resins.